Black Oxide Coating – How it Works, Benefits, and Types
In the realm of surface treatments, black oxide coating stands out as a time-honored method. It enhances the aesthetic appeal of metal components and significantly boosts their durability and corrosion resistance.
This chemical process creates a uniform black finish. Black oxide has found its place in various industries, including automotive, aerospace, and firearms, due to its ability to improve both functionality and appearance. Beyond its traditional applications, black oxide is gaining traction in modern manufacturing.
Sustainability and performance are paramount here. Companies seek innovative solutions to protect their products while adhering to environmental standards.
This article will delve into the intricacies of the coating. It will explore its definition, process, applications, advantages, and limitations. Additionally, it will shed light on why it remains a preferred choice for engineers and manufacturers alike.
What is Black Oxide Coating?
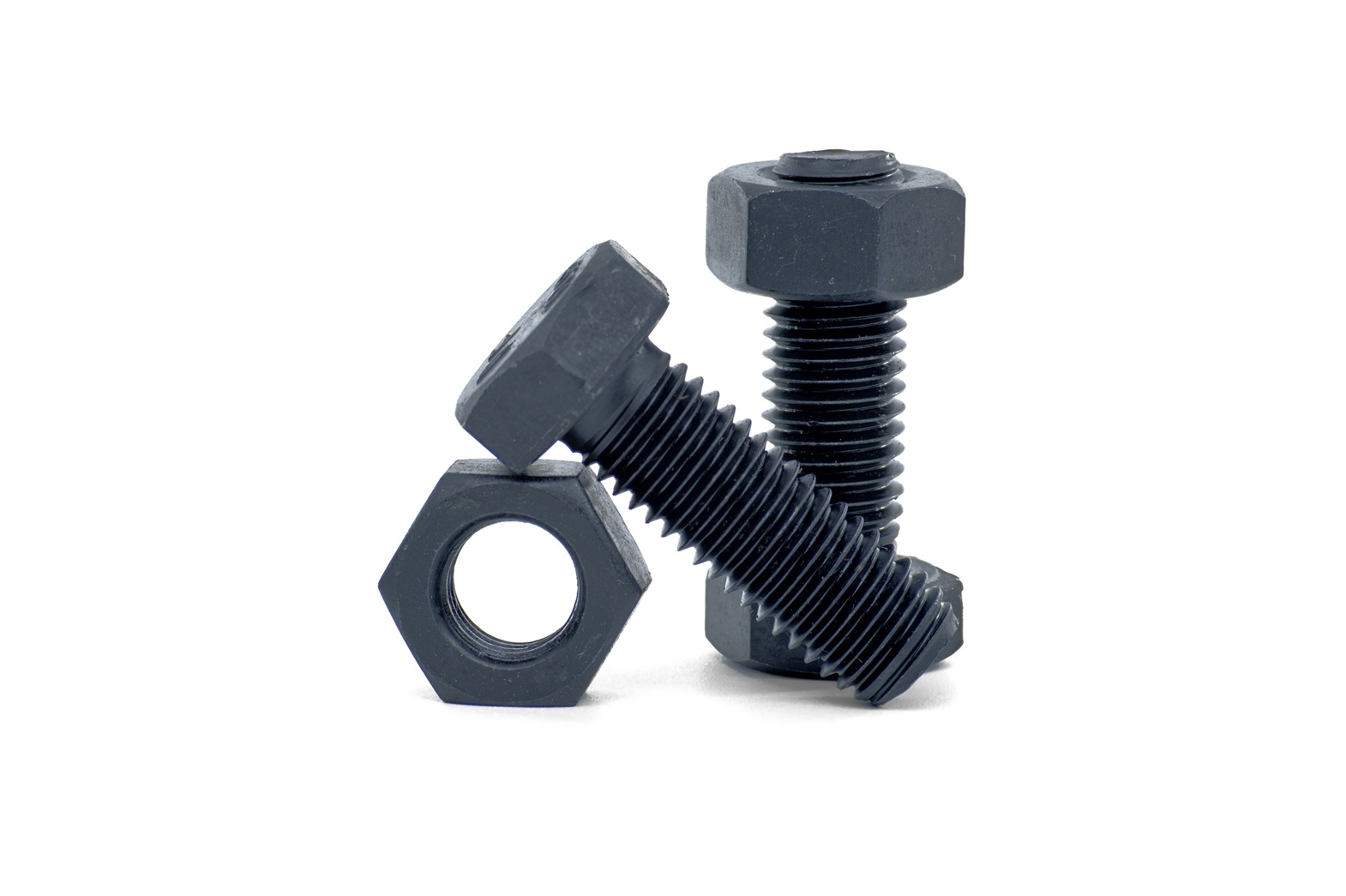
What does black oxide coating do? It’s a specialized chemical process applied to metals, primarily ferrous materials like steel and iron, to create a protective layer on the surface. Unlike coatings that involve adding a layer of material on top of the metal, black oxide chemically reacts with the metal itself.
It alters its surface to form a thin layer of magnetite (Fe3O4). This conversion process results in a sleek, matte black finish that offers mild corrosion resistance, improves appearance, and maintains the metal's original dimensions.
The distinguishing feature of black oxide coating is that it does not alter the size or shape of the treated part. This makes it an ideal choice for precision tools, fasteners, and other industrial components where maintaining exact tolerances is essential.
As a result, black oxide has become a popular choice across a range of industries, including automotive, firearms, fastening components, aerospace, and electronics.
In addition to its protective properties, black oxide also enhances the aesthetic appeal of treated parts. The rich black color, combined with a smooth finish, gives metal parts a professional, uniform look. Furthermore, when paired with a post-treatment such as oil or wax, black oxide increases corrosion and wear resistance.
The Black Oxide Process: Step-by-Step
The black oxide coating process is a carefully controlled procedure that involves several key steps to ensure proper adhesion and long-lasting results. Let’s break down each phase:
Cleaning and Preparation
The process begins by thoroughly cleaning the metal surface to remove contaminants such as oils, dirt, rust, or grease. This ensures the metal surface is free of any residue that could interfere with the chemical reaction needed to form the black oxide layer. Methods used for cleaning may include degreasing, pickling (to remove rust), or abrasive blasting.
Alkaline Bath
After the cleaning stage, the metal is submerged in an alkaline solution. This solution helps to prepare the surface for the chemical conversion process that follows. It removes any remaining impurities and ensures that the metal is in the ideal state for treatment.
High-Temperature Black Oxide Bath
The heart of the black oxide process involves immersing the metal in a heated bath (around 286°F) containing a mixture of sodium hydroxide, nitrates, and nitrites. This causes a chemical reaction that converts the outermost layer of the metal into magnetite (Fe3O4). This black, corrosion-resistant layer adheres to the surface and forms the characteristic black oxide finish.
Rinsing
Once the metal has been treated, it is removed from the bath and rinsed in water. The rinsing step is crucial to eliminate any leftover chemicals from the surface that could cause discoloration or interfere with the sealing step.
Sealing and Post-Treatment
After rinsing, the metal may be dipped in oil, wax, or other sealing solution. This step enhances the corrosion-resistant properties of the black oxide coating. Without post-treatment, the black oxide finish alone offers minimal protection against rust, particularly in harsh environments.
Sealing also improves the part's appearance and slightly increases lubricity, which can benefit moving parts in mechanical applications.
Inspection and Quality Control
The final step involves inspecting the coated parts to ensure the black oxide layer is uniform, properly sealed, and free from defects. Quality control may include visual inspection, as well as testing for corrosion resistance, adhesion, and durability.
Each step of this process is critical in achieving the desired result. While black oxide is a relatively straightforward coating option, careful execution ensures that the treated metal parts receive the full benefits of this treatment.
Applications Across Industries
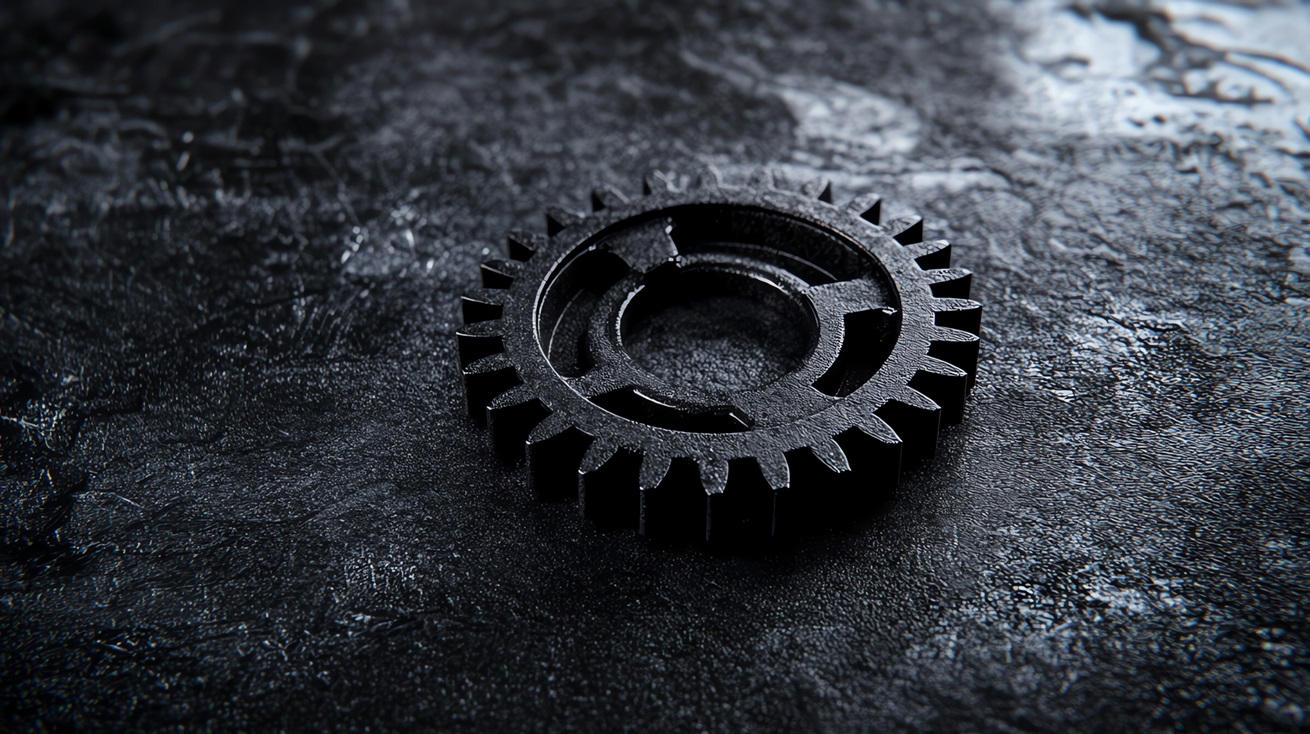
The black oxide coating process is not only favored for its functional benefits but also its sustainability. As industries increasingly prioritize environmentally friendly practices, black oxide presents an attractive option due to its relatively low environmental impact.
Unlike processes that require heavy metals or harmful chemicals, black oxide typically employs less toxic materials. Additionally, many of the chemical components used can be recycled or reused, significantly reducing waste and pollution.
This aligns with the global push towards green manufacturing, making black oxide a choice that appeals to companies aiming to enhance their sustainability credentials.
Moreover, black oxide's versatility extends beyond its traditional applications in the automotive and aerospace sectors. Emerging fields, such as robotics and automation, are beginning to adopt black oxide coatings for their components.
In robotics, where precision and durability are paramount, black oxide provides the necessary protection without compromising the integrity of intricate parts.
Furthermore, the coating’s ability to reduce glare enhances the visibility of robotic systems, making them more efficient in various operational environments. This trend indicates that black oxide is not only a time-tested solution but is also adapting to meet the needs of modern technology, showcasing its enduring relevance in an ever-evolving market.
Automotive Industry
In the automotive sector, black oxide coating is frequently applied to fasteners, gears, shafts, and other components that require moderate corrosion resistance without altering part dimensions.
These treated parts are commonly found in engine assemblies, transmissions, and chassis components, where they endure high stress and exposure to environmental factors such as moisture and road salt.
Firearms Industry
Known as "bluing" in the firearms industry, black oxide is widely used to treat gun barrels, receivers, and other firearm components. The coating helps protect firearms from corrosion while also enhancing their appearance with a sleek, professional finish.
The non-reflective nature of the black oxide coating is especially important in tactical or military settings where minimizing glare is critical.
Aerospace Sector
In aerospace applications, black oxide coating is used on a variety of precision components, including bolts, screws, and pins. These parts require corrosion resistance without affecting their dimensional accuracy, which is critical for the demanding requirements of aerospace engineering.
The lightweight, thin nature of the black oxide coating makes it an ideal choice in this high-tech industry.
Medical Equipment
Black oxide is also used in the medical field to treat surgical instruments and other medical devices. One of the primary benefits of this application is that the coating reduces light reflection, which is essential in operating rooms where bright lights can interfere with a surgeon's visibility.
Additionally, the mild corrosion resistance provided by black oxide helps extend the lifespan of these instruments.
Tool Manufacturing
Hand tools, such as wrenches, pliers, and sockets, are often treated with black oxide to increase their lifespan and improve their resistance to rust. This treatment ensures that tools can withstand exposure to moisture and harsh environments without suffering significant wear or corrosion.
Electronics and Electrical Components
Black oxide is sometimes applied to electrical components, such as connectors and brackets, to prevent corrosion and reduce electrical resistance. This helps ensure the long-term reliability of electrical systems, particularly in outdoor or industrial settings where corrosion could cause failures.
The Benefits of Black Oxide Coating
Black oxide coating offers a range of benefits that make it an attractive option for various industrial and commercial applications. Here are some of the key advantages:
- Dimensional Stability: Since black oxide is a conversion coating rather than an additive one, it doesn’t affect the dimensions of the treated part. This makes it ideal for components that require tight tolerances, such as fasteners, gears, and precision tools.
- Aesthetic Enhancement: Black oxide imparts a uniform, matte black finish to metal parts, improving their appearance and giving them a professional, sleek look. This is especially important in industries like firearms and automotive, where aesthetics play a significant role in product design.
- Corrosion Resistance: When paired with a sealing treatment like oil or wax, black oxide offers moderate protection against corrosion. This is particularly valuable in environments where parts are exposed to moisture, chemicals, or other corrosive elements. However, it’s important to note that black oxide alone provides limited corrosion resistance and is most effective when combined with a post-treatment.
- Improved Lubricity: Black oxide coatings can reduce friction between moving parts, making them suitable for use in mechanical systems where smooth operation is critical. The added lubricity helps minimize wear and tear, prolonging the lifespan of machinery components.
- Non-Reflective Surface: Black oxide's matte finish reduces glare and reflection, making it ideal for applications where a non-reflective surface is desired. This is especially important in optical instruments, military equipment, and firearms.
- Cost-Effective: Black oxide is a relatively low-cost coating option compared to other surface treatments, such as electroplating or powder coating. The simplicity of the process, combined with its effectiveness, makes it a cost-efficient solution for large-scale production.
- Environmentally Friendly: Black oxide coating generates minimal hazardous waste compared to other metal finishing processes. Many of the chemicals used in the process can be recycled, and the process does not produce harmful emissions or heavy metal waste.
Limitations of Black Oxide Coating
While black oxide coating offers numerous advantages, it also has some limitations that should be considered before choosing it for a particular application:
- Limited Durability: Black oxide is not as durable as other coating methods, such as powder coating or electroplating. While it offers moderate corrosion resistance, it does not provide significant protection against mechanical wear or heavy abrasion. In environments where parts are subject to extreme wear, black oxide may not be the best choice.
- Low Corrosion Resistance Without Sealing: The base black oxide layer provides only minimal corrosion resistance on its own. For enhanced protection, parts must be treated with a post-sealing process using oil, wax, or another protective coating. Without this additional step, black oxide-coated parts may rust in humid or corrosive environments.
- Not Suitable for All Metals: Black oxide is most effective on ferrous metals like steel and iron. Non-ferrous metals, such as aluminum, brass, and copper, require alternative blackening processes that may not achieve the same level of uniformity or corrosion resistance.
- Temperature Sensitivity: The black oxide process involves high-temperature chemical baths, typically around 285°F to 295°F. This makes the method unsuitable for heat-sensitive materials or parts that cannot withstand high temperatures.
Benefits vs. Limitations: A Summary Table
Benefits | Limitations |
Dimensional stability | Limited durability |
Aesthetic enhancement | Low corrosion resistance without sealing |
Moderate corrosion resistance | Not suitable for all metals |
Improved lubricity | Temperature sensitivity |
Non-reflective surface | |
Cost-effective | |
Environmentally friendly |
Summary
This comprehensive guide covers all aspects of black oxide coating, offering a detailed exploration of its process, applications, benefits, and limitations. It also includes practical, real-world examples and a concise summary of its pros and cons.
Frequently Asked Questions (FAQ)
Q: How thick is a black oxide coating?
A: Black oxide coatings are extremely thin, usually measuring between 1 and 2 microns in thickness. This minimal thickness ensures that the part’s dimensions remain unchanged.
Q: Can stainless steel be treated with a black oxide coating?
A: Yes, there’s a specific process for making black oxide stainless steel. The process is slightly different from the traditional black oxide used on carbon steel.
Q: Is black oxide coating permanent?
A: Black oxide coatings are permanent. They offer lasting protection when combined with a post-treatment.